Corrosion protection of metal should be one of the priority values for any manufacturer of garden architecture. In this article we want to introduce the most commonly used protections for steel and aluminum surfaces. We will compactly discuss their properties, methods of application and factors affecting corrosion.
Types of coatings and the most popular anti-corrosion systems we will discuss in this article
- Hot-dip galvanizing (hot-dip galvanizing)
- Galvanization (zinc plating, electroplating)
- Geomet
- Powder coating
- Powder coating + zinc primer
- Chemical painting
- Chrome coating
- Anodizing
- Polymer coatings
- Copper coating
Corrosion protection of metal components, anchors, slings or fittings against corrosion or other external factors is extremely important. It largely determines the quality of our construction. To ensure the durability and functionality of the structure created using these elements, anti-corrosion coatings must be selected according to the type of material and operating conditions.
It is well known that metal used in construction, although durable, is susceptible to moisture, pollution, salt or even changing weather conditions. These are just some of the factors that affect corrosion. In garden architecture, where metal mounting systems are subjected to heavy loads, it is important to properly protect the metal to guarantee many years of stability for the entire structure.
The use of protective coatings significantly extends the life of metal components, reducing frequent replacements, maintenance or possible repairs.
The most commonly used types of anti-corrosion coatings
In this section we will discuss and characterize the most common anti-corrosion protective coatings. You will learn about their characteristics and under what circumstances they are best used.
Hot-dip galvanizing - good and inexpensive protection of garden architectural elements
It is a process in which the metal is coated with a layer of zinc to protect the steel from corrosion. It involves immersing steel parts in molten zinc, the temperature of which is about 450 °C. During this time, the zinc adheres to the entire metal component, forming an anti-corrosion layer.
The coating protects the components from the wet or salty environment in which such fixings are often found. The coating is impermeable to water and air, so there is no degradation process. This prolongs the life of steel components.
This form of rust protection works well for many types of fastening systems, such as. anchors, finials for gazebos or pole supports.
Galvanizing - popular for smaller steel structure components
A process also known as electrolytic galvanization or electroplating, during which a thin layer of zinc is applied to a steel component using an electric current. The metal parts are immersed in a special chemical solution, the main ingredient of which is zinc salt, and then an electric current is passed through them. Through these steps, zinc is deposited on the metal surfaces to form a protective coating.
This type of corrosion protection is most often used for smaller steel components, such as: screws, fittings, angle fasteners or slings.
Geomet coating - effective and durable protection against corrosion
An interesting alternative to traditional galvanizing. In this process, a metal component is immersed in an electrolytic solution consisting of zinc, copper and aluminum. An electric current is passed through the solution. As a result, fine particles of the aforementioned metals adhere to the surface of the component, forming a protective layer. Then, after the coating is deposited, the elements are subjected to curing and high-temperature drying. Thanks to this, the element will gain durability and above-average corrosion resistance.
This protective coating is most often used on undersized metal parts that will be used/exploited frequently, such as. slings for swings for public playgrounds.
Powder coating - aesthetic appearance and protection of steel structures
A durable and highly aesthetic way to protect metal, it has many applications. Here, a special powder paint is applied to metal surfaces using electrostatic charging. The powder paint adheres to the component, and then the entire component is put into an oven to cure. At 160°C a 200°C, the powder melts and a smooth protective layer is formed. The time for such curing in the oven takes about 10-20 minutes, depending on the thickness of the paint layer to be applied.
The resulting coating guarantees a high level of protection for the metal component, while also making it look very aesthetically pleasing. Powder coatings are available in RAL colors. It's a huge plus that we can have the element in the color of our dreams. This corrosion protection has an added bonus: the painted element can be in a smooth gloss or a slightly rough matte texture.
Below photo: 1. Stucture, 2. Smooth sheen
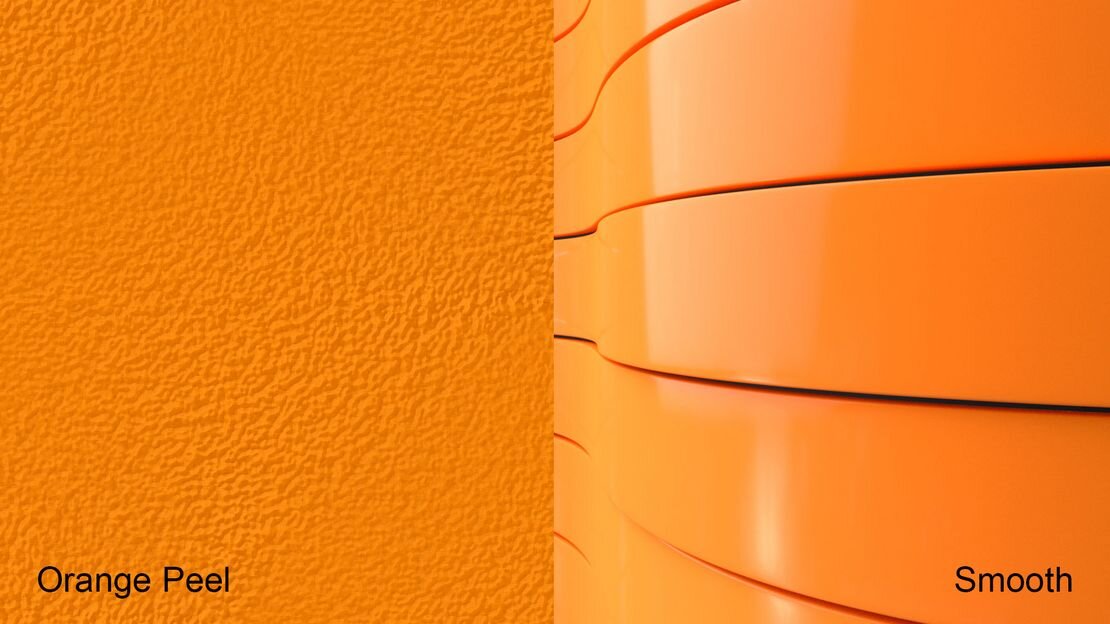
Powder coating not only provides permanent protection against: corrosion, but also scratches. Thanks to the paint layer, it is more difficult to mechanical damage. The coating is resistant to changing weather conditions, such as: rain, snow and UV radiation.
Such protection of steel surfaces is used for climbing rods, fire-fighting pipes, ladders or connectors for swings.
Powder coating + zinc primer - double corrosion protection
This is a strong combination! Double protection of metal elements, very effective anti-corrosion protection. Zinc primer applied to the surface of the metal already creates a protective layer, and if such an element is painted with powder paint we have a guarantee of extraordinary durability and resistance to changing weather conditions. In addition to corrosion protection of the structure, we also gain the opportunity to choose any color from the RAL palette.
Chemical painting - protective painting systems
This is a type of metal protection that uses polyurethane paints, acrylic paints, epoxy paints, chlorinated rubber paints. The right anti-corrosion paint applied to the surface forms a protective system against rust, seals and ensures the durability of the metal component.
Painting steel structures is an effective protection against rust. It is important to clean the metal before painting and properly prepare the surface (such as degreasing the metal). Painting effectively preserves steel structure components already in use. Some paints can be applied directly to rust (although, if possible, it is recommended to prepare the surface in advance, cleaning, removing flaking rust)
Ways to protect aluminum - anodizing
This is another way to protect metal parts. Anodic coatings are particularly popular for protecting aluminum from external conditions.
Anodizing is an electrolytic process that produces an oxide layer on the surface of aluminum. It increases hardness and abrasion resistance. In addition, anodizing improves the appearance of aluminum, giving it an elegant matte finish available in many colors. And how is it formed?
The cleaned metal is immersed in an electrolyte solution (usually sulfuric acid) and subjected to an electric current. After such a step, a layer of aluminum oxide is formed on the surface of the metal, which is durable, transparent and resistant to corrosion. After the anodizing process, the metal becomes slightly porous, which allows dyes to be absorbed and give the aluminum the color of its choice.
Polymer protective coatings - painting of steel structures
These are coatings of polymer paints, such as epoxy, polyurethane or PVC paints, which protect the metal from weathering and chemical agents by being applied to the metal surface (by brush, spray, dip or powder). The coating is then cured in an oven or left to dry.
Chrome coating
Chrome coating is a thin layer of chromium applied to a metal component, which is designed to protect the component from corrosion, while significantly improving hardness. It makes the metal more resistant to abrasion and mechanical damage.
There are two methods of coating: galvanic chromium plating (electrochemical) and vacuum chromium plating (PVD technology).
Galvanic chromium plating, involves immersing the metal in an electrolytic bath consisting of potassium chromate and then passing an electric current. As a result, chromium is deposited on the metal component, creating protection against corrosion. Vacuum, involves sublimation of chromium in a vacuum environment. The vapor produced from the chromium is deposited on the metal component, providing a thin layer/coating that protects against abrasion and rusting.
Chromium plating as surface corrosion protection is used more in the automotive, home furnishings, aerospace industry. In the field of garden architecture manufacturers it is not encountered, because it is quite a lot more expensive than, for example, galvanizing.
Copper coating
This protection process involves applying a thin layer of copper to the metal to increase corrosion resistance, especially in electronic devices. The metal component is immersed in a solution containing copper salts and then an electric current is passed through it. Deposition of copper on the metal's surface occurs. Copper anti-corrosion protective coatings are unlikely to be used on large pieces of garden architecture.
Factors affecting corrosion?
It is no secret that the durability of steel structural components depends on the environment in which it is located. That is why surface corrosion protection is so important and must be selected according to the conditions. For garden architecture and backyard playgrounds, powder coating and hot-dip galvanizing are the most common options. And what factors do we need to take into account?
- Humidity - it is known that the wetter it is, the faster corrosion of steel structures progresses. Components require regular maintenance, more frequent than in drier regions
- salinity - the protection of steel structures in coastal areas, exposed to salt carried by the wind, must be very solid and regularly maintained. The situation is similar with elements of small architecture located near roads - exposed to contact with road salt
- Acidic environment - this can be about acidic soil, but also heavily polluted air around roads, city centers, industrial areas. Smoke and exhaust fumes can react with rain to form so-called acid rain
- intensive use - heavy loads and frequency of use can mechanically damage or abrade the protection of steel structures. A chip in the galvanizing or a scratch on a powder-painted surface must be quickly located and secured. Otherwise, it can become a focus of corrosion
Corrosion protection according to ISO 12944 - why is it so important?
Protective coatings perform a very important function in protecting metal fasteners of garden architecture, mainly from damage and adverse weather conditions. Of course, not all of the types of protective coatings described above have practical applications in garden architecture. We wanted to show you how important it is to choose products with a protective coating and how this affects their aesthetics and durability. A special standard has even been developed to regulate corrosion protection systems. Products with protective coatings that meet the EN ISO 12944 standard will last a really long time when used correctly.
Sound surface corrosion protection is not a small thing we can overlook or neglect. It minimizes the possible costs of maintenance, damage during long-term use. For manufacturers of backyard playgrounds and garden architecture, this should be a priority, as it will avoid complaints. And a well-made investment and customer satisfaction is the best advertisement in the industry!